Near Zero Steel 2030 Challenge: Top Innovators
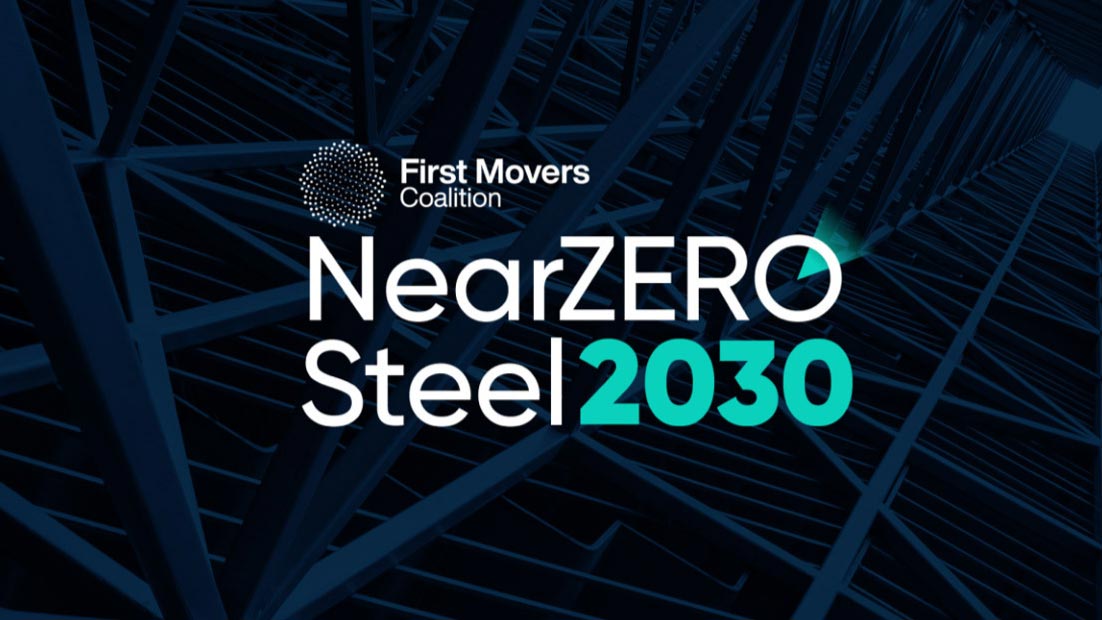
Decarbonising the steel industry is a crucial challenge to overcome if the world is going to meet its climate goals. Steel production contributes around 11% of global carbon dioxide (CO2) emissions, making it one of the heaviest polluting industries and a heavy-emitting sector of focus for the First Movers Coalition, an initiative seeking to aggregate demand for near-zero emissions products and services across some of the world’s most polluting industries.
The coalition’s mission is to drive investment and accelerate the scaling of the breakthrough technologies required to make these products by demonstrating a credible demand signal for highly decarbonised products.
But how can these innovative technologies be surfaced and scaled? The First Movers Coalition’s near zero steel challenge was a recently concluded global initiative by the World Economic Forum and Greenhouse, with support from partners Boston Consulting Group, Deloitte, ResponsibleSteel and RMI. It aimed at identifying which companies will supply final steel products at First Movers’ near-zero emissions thresholds by 2030, which companies seek to buy these steel products and which companies are providing the enabling technologies for highly decarbonised steel production.
The 70 submissions to this latter challenge of enabling technologies showcase solutions across several sub-categories that steel producers require to produce near-zero emissions steel. An expert evaluating panel whittled the 70 submissions to 17 top innovators based on relevance, feasibility, scalability, technology readiness and impact, with each technology sub-category having a top-ranked entry.
Carbon Capture Technologies
Molten Industries
Molten’s methane pyrolysis technology produces carbon-neutral hydrogen and graphite in a continuous process at >1000C using 4x less electricity than water electrolysis. Molten uses existing natural gas infrastructure to provide a scalable, cost-efficient solution for steel producers, delivering a continuous stream of hot hydrogen for direct reduced iron (DRI) furnaces, blast furnaces, or annealing furnaces.
Hydrogen Green Energies Private Lim
It develops and deploy scaled-up commercially attractive Green Hydrogen and derivatives (e.g. Green Ammonia, Bio-Fuels) production assets on Build-own-operate / Gas-as-aService basis. We are on the verge of deploying India's first commercial long term offtake green hydrogen plant in Jindal Stainless, based in Hisar India. With this, we are going the revolutionise the used of Green Hydrogen in Steel Making.
Invenergy LLC
The world’s leading privately held developer, owner, and operator of clean energy with over 31 GW developed, offers clean power and clean hydrogen for green steel production. It has executed over 5 GW of contracts with commercial and industrial customers, will be operating its first hydrogen plant in Q1 2024 and is developing other clean hydrogen projects. Combining hydrogen Direct Reduced Iron.
8 Rivers
The 8RH2 hydrogen production process achieves >99% CO2 capture at lower capital and operating costs than its peers by employing 8 Rivers’ CO2Convective Reformer (CCR) technology. The process uses natural gas as a fuel and a feedstock. In addition to hydrogen production, 8RH2 can coproduce power and heat. Therefore, the process can provide decarbonised power, heat, and hydrogen to several steelmaking steps at industrial-scale while continuing to use affordable, reliable and secure feedstocks.
KC8 Capture Technologies
KC8’s carbon capture solution is retrofittable to large scale emissions sources, benefitting from its unique advantages of smaller footprint. UNO MK3 is an innovative development of a long-standing inorganic solvent absorption process. This novel technology is more environmentally friendly and significantly more cost-effective (up to 50% less) than the amine processes in current carbon capture applications. The environmental benefits are due to the use of potassium carbonate.
Lanza Tech
Our gas fermentation platform diverts the emissions from Blast Furnaces which are rich in CO and processes them using a nature based solution much like traditional fermentation, to make chemicals. This enables steel mills to turn a liability (emissions) into an opportunity (new value chain). This is more efficient than combusting for power and allows customers to realise value from ethanol (our primary product) and its downstream applications (PET, PE etc), while reducing overall emissions and pollutants at source.
MCi Carbon
MCi Carbon can offer a carbon capture and use solution which transforms CO2 into saleable materials. This process of reacting CO2 with minerals usually occurs over millions of years geologically but MCi have developed technology to accelerate that process for use in industrial settings. MCi reacts CO2 with a mineral feedstock, usually an industrial waste like steel slag, mine tailings or raw quarried minerals, to produce magnesium carbonate, calcium carbonate and/or amorphous silica.
Direct Reduction
GravityHy
An innovative power to iron business model to provide lowcarbon and green hydrogen based direct reduced iron (DRI/HBI) to support and accelerate the defossilisation of the steel industry. It disrupts the value chain by building, owning and operating H2 based DRI/HBI production facilities, thus decoupling iron and steel making and optimising value creation along the way. The low-carbon DRI/HBI produced will be accessible to all steel-making stakeholders wishing to reduce the related GHG emissions of their products.
Calix Ltd
Zero Emissions Steel Technology (ZESTY) enables the direct reduction of iron ore to iron and steel products with near zero emissions. ZESTY uses electricity to heat reactor tubes and deliver radiative heat to iron ore with precise temperature control. Indirect heating ensures that hydrogen is used only as a reductant – it is not combusted or used as a fuel, and any unused hydrogen can be simply recycled. This unique feature enables ZESTY to target the minimum possible use of hydrogen in the reduction of iron ore.
Biochar
Biochar is a technology and process that produces a 100% net zero fuel (biochar) for steelmaking. This is used as a replacement for coal and coke in the steelmaking technology that dominates 99% of the market. Allowing thousands of blast furnaces to significantly reduce their carbon emissions without having to invest significant time, capital and risk associated with emerging green steelmaking technologies. Our biochar is either bended with coal/coke before use as the reductant.
Helios
Helios introduces the “Helios Cycle”, a novel technology for iron ore reduction process substituting sodium for carbon. The Helios Cycle, which can also apply to low-grade ores, yields metallic iron powder, which can later be briquetted. The process has no direct CO2 emissions, with oxygen being the only byproduct besides gangue-related compounds. The reducing agent is thermally recycled, ensuring a cost-effective, sustainable, and environmentally friendly solution.
Electrolysis
Boston Metal
Boston Metal is commercialising Molten Oxide Electrolysis (MOE), a tonnage metals technology platform powered by electricity, to decarbonise steelmaking and transform how metals are made. MOE provides the metals industry with a scalable, cost-competitive and green solution for the production of steel and high-value metals from a variety of feedstocks and iron ore grades. Backed by visionary investors and led by a world-class team, Boston Metal is headquartered in Woburn.
Jolt
It has developed a patented industrial catalytic coating process to manufacture high volume/low cost/ high performance electrodes for use in hydrogen electrolysers (and other forms of electrolyser and redox flow batteries) that will help the production cost and scaling issues facing green hydrogen. Our SPARKFUZE process introduces a 21st century standard for catalysis and protective coatings, unlocking green hydrogen & decarbonising industry. It is easy to integrate in your industrial operation.
Plug Power
Plug is both a manufacturer of electrolysers as well as a supplier of hydrogen-as-a-gas. Steel industry looking to decarbonise its steel production pathways via hydrogen, Plug believes we can tailor solutions that fit our customer’s needs who need a dependable source of low-carbon hydrogen for their operations. Current customers of our electrolysers are using the equipment to produce hydrogen for their industrial application, varying from heat production to oil and gas refining, or for the mobility market.
Elogen
It is a leader in PEM (proton exchange membrane) electrolysis. We provide solutions for mobility projects, energy storage, light and heavy industries like steel industry. Our PEM electrolysers are equipped with stacks from our own development and production on our own production lines. We are one of the few companies awarded a IPCEI project which will boost our electrolyser production capacity to multi GW per year.
Hedean Energy
This solution aims at providing the lowest levelised cost of hydrogen for hard to abate sectors, such as steel making. Hadean produces the individual cells and designs the modular electrolyser bundle (stack), which can then be mass manufactured and integrated into industrial processes. Green steel producers can use waste heat as a feedstock into the electrolyser, reducing the electrical energy required to produce hydrogen. Similarly, waste CO2 can be captured .
Power to Hydrogen (P2H2)
P2H2 makes an electrolyser that is optimised for renewable energy integration. Electricity cost typically makes up ~75% of the cost of a kg of hydrogen. While some companies pursue optimiwing electrical efficiency in electrolysis, P2H2 believes there’s a greater opportunity to reduce the cost of clean hydrogen with renewable energy integration. P2H2’s AEM electrolywers are optimiwed to produce hydrogen from renewable energy.
Furnace Technology
Coolbrook Oy
Roto Dynamic Heater (RDH) technology is for electrification/ decarbonisation of high-temperature industrial process heating up to 1700 C degrees. By replacing the need to burn fossil fuels with clean electrification, it can decarbonise high-temperature processes in traditionally hard-to-abate heavy sectors, such as steel, cement, pulp ; paper. RDH technology thus replaces the burning of fossil fuels which currently used for heating.
University of New South Wales
Shen Lab, UNSW has patented the co-injection of hydrogen and biomass technology to facilitate the transition towards greener ironmaking. Our technology requires minimal investments and modifications, allowing steel companies to employ it until zero-carbon ironmaking technologies mature sufficiently. Hydrogen, known as a carbon-free fuel, effectively reduces carbon emissions during blast furnace operations.
BioCarbon
BioCarbon has developed renewable carbon products for Electric Arc Furnace (EAF) steelmaking. Our innovative pyrolysis technology produces high quality char at low cost. Char is processed into products that replace fossil coke, with no changes to normal EAF operation. The carbon products have been successfully trialled with two EAF operators in multiple heats. The most recent trial has produced 1,000 tonnes of steel without using coal based, charge coke.
Clean Hydrogen
Xi'an LONGi Hydrogen Technology
It has launched a "Green Power+ Green Hydrogen" system solution to help customers and the market quickly improve project solutions. From green power to green hydrogen, we find the optimal solution for LCOH for our customers. The main advantages of the "GreenPower+ Green Hydrogen" system solution are safety, reliability, efficiency and flexibility. It solves the major pain points of green hydrogen project economic calculation, difficulty in selecting the best solution, difficulty in adapting to fluctuating power.
Hydrogen Waves (HyWaves)
HyWaves' power management and control architecture avoids the multiple power conversion stages by directly connecting the electrolyser stack with a solar PV array or DC green energy source, producing green H2 up to 10% more efficiently and more than 20% cheaper, replacing costly power electronics with a robust, low-cost system adaptable to suit a range of commercially available hydrogen electrolysers. The HyWaves approach is aimed at dedicated co-located renewable energy (e.g. Solar PV, Wind turbine).
Orcan Energy AC
Develops, produces, distributes energy modules for the conversion of waste heat into clean and affordable electricity and constructs them on a turnkey basis, including the installation required for waste heat extraction. Its products tap into the enormous global waste heat potential and enable customers to save CO2 emissions and costs at the same time. It unlocks the energy potential of unused heat sources based on second-generation Organic Rankine Cycle (ORC) technology.
Become an important part of climate innovation in Australia
We're building an ecosystem to accelerate climate innovation. Want to be a part of it?
Become an important part of climate innovation in Australia
We're building an ecosystem to accelerate climate innovation. Want to be a part of it?
Book your next meeting at Greenhouse
Take your ideas to the next level in our state-of-the-art space in Sydney's CBD.
Book your next workshop at Greenhouse
Take your ideas to the next level in our state-of-the-art space in Sydney's CBD.
Book your next event at Greenhouse
Take your ideas to the next level in our state-of-the-art space in Sydney's CBD.
Join a community of climate innovators
Become a member of our growing Greenhouse community in Sydney's CBD.
Join our partner ecosystem
Get inside access to climate innovation and help us accelerate the development and deployment of climate innovation.